硫化階段
從硫化時間影響膠料定伸強度的過程來看,硫化是由幾個反應階段組成的:焦燒或硫化起步、欠硫、正硫和過硫。天然膠在最后一個階段往往有“返原”的特點。各階段如圖4所示。
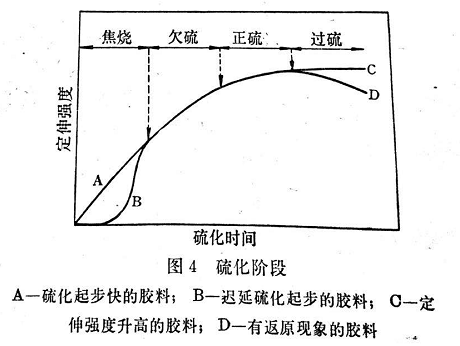
硫化起步
所謂硫化起步是指膠料開始變硬,從此不能進行熱塑性流動那一點的時間。在平板加壓硫化中,這個起步隨著硫化助劑的不同可以出現得早些(如用超促進劑),也可以出現得遲些(如用次磺酰胺類促進劑)。平板加壓硫化時,為使模型全部充滿膠料,必須在硫化起步前有一較長的時間使膠料處于流動狀態。但在無模硫化中,硫化起步應盡可能早一些以使制品在硫化中盡量保持原形。因為膠料硫化起步快而迅速變硬,可以防止制品受熱變軟而產生變形。當然,在大多數情況下不希望硫化起步過早,免得對膠料操作安全不利。顯然,一個較遲的硫化起步能夠減少操作期間的焦燒趨向,并能提高溫度使配煉和成型能在沒有焦燒危險的條件下進行。這一點對于合理化措施十分重要。在一定程度上,只有膠料經過調整使之有足夠遲的硫化起步時,才有可能使用一些加速硫化的原料(如爐黑),或者使用一些加工溫度特別高的配合劑。因此,實際上現已漸漸傾向于使用遲延硫化起步的促進劑,例如次磺酰胺促進劑,或加入防焦劑。
硫化開始時,膠料仍不是很強韌的,嚴格地說,還不能稱為硫化膠。有輕微焦燒現象的膠料有時可以譬如用防焦劑使其重新塑化。但通常只能再予以硫化并研碎之后用作碎膠。
欠硫
硫化起步和正硫化之間的階段稱為欠硫。在這一階段中,抗張應力隨硫化時間有很大增加。由于這時交聯度仍然很低,橡膠制品應具備的性能大多還不明顯,所以,高度欠硫的制品沒有工業價值。
這種制品的抗張強度低,伸長卻相當高,永久變形也非常大,甚至一個指甲印也會留下形變,而成為高度欠硫的明顯標志。這種硫化膠的老化性能也比較差。
制品輕微欠硫的情況有所不同:抗張強度、彈性和抗張應力仍不理想,扯斷伸長也比較高,但硫化膠的抗撕裂性能、耐磨耗性能和動態裂口都優于正硫化膠料。因而如果后面幾種性質特別重要時,制品可以輕微欠硫。換言之,可以犧牲一部分抗張強度和彈性以換取良好的抗撕裂、耐磨耗及改進裂口性能。
正硫化
在多數情況下,制品的硫化都必須使其達到適當的交聯度——正硫化。值得注意的是,在工藝上的正硫化并非抗張應力硫化時間曲線的最高點,而實際是在其稍低的地方。已經發現,當硫化達到抗張應力最高點或者超過這一點時,則產品的老化性能已經降低。這將在下一節詳細討論。關于確定正硫化,已經提出多種方法。
在指明的正硫化抗張應力范圍以內,工廠可以根據橡膠制品的要求,追求抗張應力低一點或硫化度高一點。如1.1.2.11節所述,因為在一定的硫化程度下,并非所有性質都是最合適的。
硫化平坦和過硫
多數合成膠在正硫化后,抗張應力仍繼續稍微上升,甚至選擇的硫化時間比較長也是這樣。因此說這種橡膠有抗張應力上升的特點。但天然膠超過正硫化時,交聯產生返原,返原速度取決于硫化體系的選擇,這種“返原”現象使機械性能受到損害。根據返原產生的快慢,定伸強度與硫化時間曲線有一段或窄或寬的平坦部分。平坦部分的寬度表明膠料熱穩定性的好壞,因為它代表硫化熱對機械性能的影響。有時抗張應力有上升的特點,另外,也有時這一曲線又幾乎與橫座標平行。
平坦部分的形狀可以基本上決定硫化膠的老化性能,而它本身在很大程度上則依賴于硫化劑的選擇及其用量。
促進劑類型和用量的差異可導致多種交聯鍵的形成,而交聯鍵鍵能相互之間也有顯著差別,在下面將加以討論。交聯鍵的大小決定膠料的熱穩定性,并因而決定膠料的返原性能。
返原現象由兩個重疊的反應所構成,即由硫化溫度所引起的交聯或(可能的)環化反應和解聚反應(見圖5)。實際的硫化曲線是由這兩個反應曲線合并而成的。曲線(a)代表形成的總交聯鍵數,曲線(b)代表斷裂的交聯鍵數,這都是從理論上推想的。硫化曲線(c)是從曲線(a)中減去曲線(b)得到的(曲線(b)是兩組曲線共用的,因為假定它們熱穩定程度是相同的)。
硫化起步后的交聯速度與促進劑的類型和用量有關。
當單獨采用熱穩定性很高的促進劑時(如胍類或其他堿性促進劑),僅就正常硫化時間而言,交聯-硫化時間曲線(圖5中以虛線表示的硫化曲線)基本上是一條直線。因此,隨硫化時間增加而形成的交聯鍵數量大體上與硫化時間成正比。
當采用熱穩定性較低的促進劑時(如秋蘭姆類促進劑)繼硫化起步之后,交聯速度一開始就比較快,這表現為硫化曲線有一陡然上升的部分。當一部分促進劑因游離基分解或去活化作用而失效和用于交聯的游離硫減少時,硫化速度即越來越慢。因此,代表交聯鍵形成之曲線(a)隨硫化時間的延長而逐漸平行,最后逐漸平行于時間軸(圖5中的實線)。
注:橡膠硫化的硫化平坦和過硫階段未完待續。